MedTech – Made of Light
What if Advanced 3D Printing Could Transform Medical Devices?
Developing new medical technologies and treatments requires extensive research and rigorous testing processes. Superior material properties and precise manufacturing are critical for implanted devices. Replicating the intricate functionalities of biological systems in medical devices is exceedingly challenging. Xolography offers a fundamentally new way of creating medical devices.
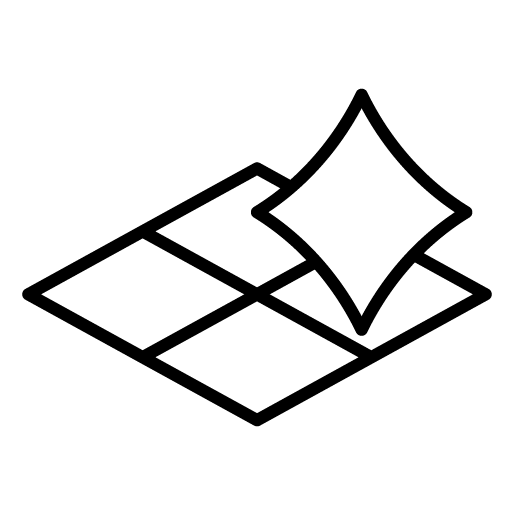
Smooth Surfaces
Surfaces of print objects are unparalleled with a minimum surface roughness right after printing. No polishing or coating needed.
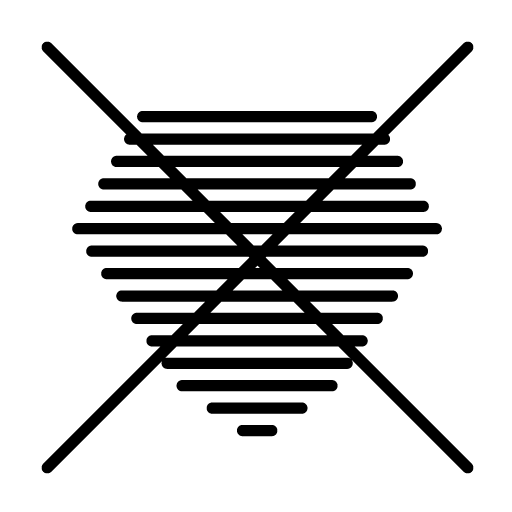
No Layers
Xolography prints the object continuously, thus avoiding layers and directional material properties.
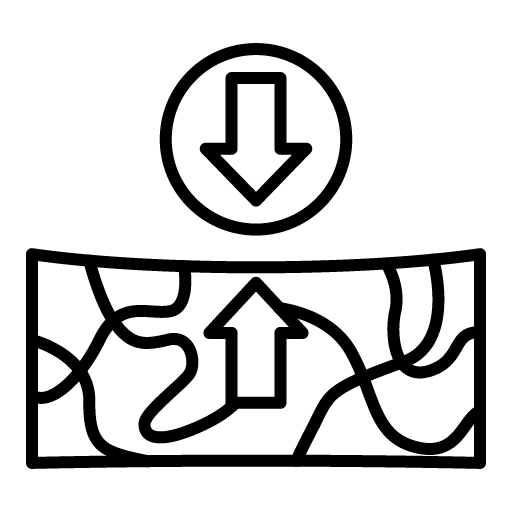
Direct Oligomer Printing
Oligomers are highly viscous materials that allow for better mechanical properties in bio-compatible parts.
How Xolography Opens Up New Potentials in MedTech
Advanced printers can create medical devices with intricate designs and superior material properties, essential for implanted devices. Today's challenge is to replicate the complex functionalities of biological systems.
Xolography's innovative approach allows for precise fabrication of devices, potentially replacing traditional manufacturing methods. The high viscosity of resins used in this process enables the use of a wider range of material options, enhancing the durability and functionality of medical implants. This could lead to safer, more effective implants and accelerate the development of medical technologies, saving time and lives.
Status Quo
3D printing in medical technology is used for creating precise implants and surgical instruments. Traditional methods fail due to material limits, imperfect fits, and lack of customization. Xolography's advanced technology offers higher accuracy, smoother surfaces, and a wider range of materials, enabling personalized and more effective medical devices.
With Xolography
Xolography overcomes 3D printing limitations with volumetric printing, eliminating layers for smoother surfaces and precise fits. It enhances durability and functionality, rapidly processes high-viscosity materials, and allows for precise customization of medical devices. Utilizing Xolography gives companies a tremendous competitive edge for many MedTech applications.