Optics - Made of Light
What if Opticians Printed Ophthalmic Lenses On-Site?
Highly individualized optical elements are essential for sensors, endoscopes, AR/VR technologies, and vision correction. Conventional optics manufacturing is labor-intensive and costly, while current additive manufacturing methods lack the precision and speed needed for optics fabrication, often requiring complex reworking of optical surfaces. Xolography introduces a paradigm shift: enabling the additive fabrication of complex optical elements within minutes, with optical-grade surfaces right out of the printer.
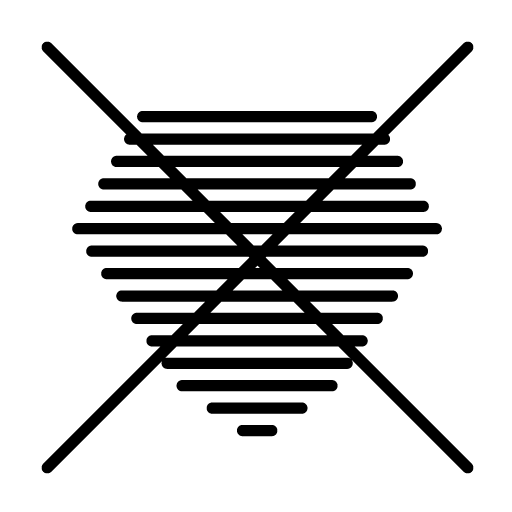
No Layers
Xolography prints the object continuously, thus avoiding the “staircase effect” on curved surfaces, eliminating the need for time-consuming reworking of the prints.
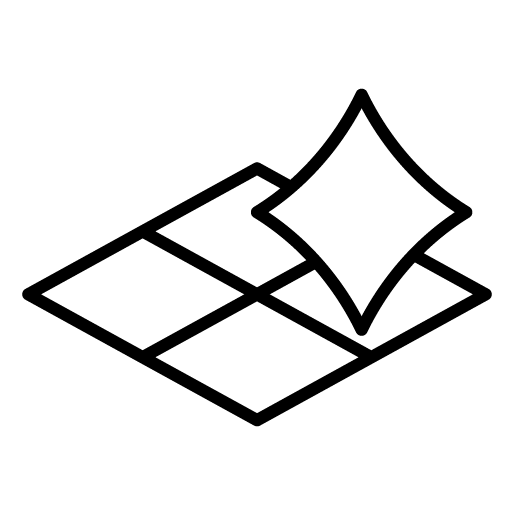
Smooth Surfaces
Surfaces of print objects are optical grade with a minimum surface roughness right after printing. No polishing or coating needed.
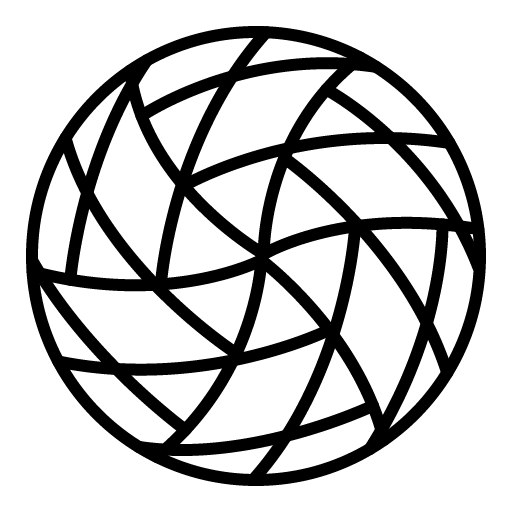
Isotropic Properties
Mechanical and optical properties of printed objects are isotropic without any layer boundaries or other internal interfaces, avoiding unwanted scattering of light.
How Xolography Opens Up New Potentials in Optics
Additive manufacturing of optical elements with speed, precision, and optical-quality surfaces is a game changer for the optics and photonics industry. Imagine designing a freeform lens for your sensor application and being able to prototype and test it within minutes. Imagine fabricating lenses and lens stacks with complex geometries straight out of the printer, without geometry restrictions or laborious assembly. Imagine producing microlens arrays without the need for expensive mastering or tooling. Imagine mass-fabricating ophthalmic or intraocular lenses, each highly individualized to the needs of your patient.
Today, individualized optical elements are produced conventionally through turning, milling, and polishing, which restricts optical surface geometries, results in long fabrication times, and generates material waste. Mass production of lenses by injection molding offers limited precision and requires expensive tooling.
Additive manufacturing of optical elements would significantly speed up prototyping and enable the production of complex geometries unattainable through conventional methods, all at economic costs.
However, todays AM technologies face serious problems in producing optical-grade parts. Layer-based processes, such as Stereolithography (SLA) and Digital Light Processing (DLP) lack the required surface quality due to the “staircase effect”, making laborious post processing of the part’s optical surfaces necessary. Inkjet Printing (IP) can produce optical parts by smoothing out surfaces during the printing process based on the wetting behavior of the deposited material. However, Inkjet Printing generally uses ultra-low viscous polymer resins, which limits the attainable optical and mechanical properties of the final printed part. Only Two-Photon-Polymerization (2PP) as a layer-less printing technology is able to produce optical-grade parts right out of the printer. However, fabrication times for larger parts become extremely long and investment costs for the printing hardware are high.
Xolography prints optical elements volumetrically, which implies printing without any geometry restrictions at an extremely fast speed. Most importantly, due to the continuous nature of the printing process, the final part does not possess layers and its surfaces do not show the “staircase effect”. Thus, optical elements printed by Xolography show optical-grade surfaces right out of the printer, making any additional reworking unnecessary.
We are working on the printing of optical lenses of various sizes, ranging from highly integrated microoptical elements and microlens arrays over macroscopic freeform optics to ophthalmic lenses, contact lenses, or intraocular lenses for the human eye. Furthermore, volumetric optics printing allows us to print both on and around other functional parts such as laser diodes, lightguides or diffractive optical elements. This will enable the highly integrated fabrication of optical devices and sensors without the need to assemble individual components.
Status Quo
Optical elements are made by turning, milling, and polishing, limiting shapes and wasting material. Injection molding is precise but costly. Additive Manufacturing speeds prototyping and allows complex shapes but struggles with optical-grade parts and need complex post processing. 2PP makes high-quality parts but is limited to nano & micro-scale, slow and expensive.
With Xolography
Xolography prints optical elements volumetrically, without geometry restrictions, at high speeds. The continuous process eliminates layers and the "staircase effect," producing optical-grade surfaces without reworking. We print lenses of all sizes and around functional parts, enabling integrated optical devices without assembly.